Joshua Asbury
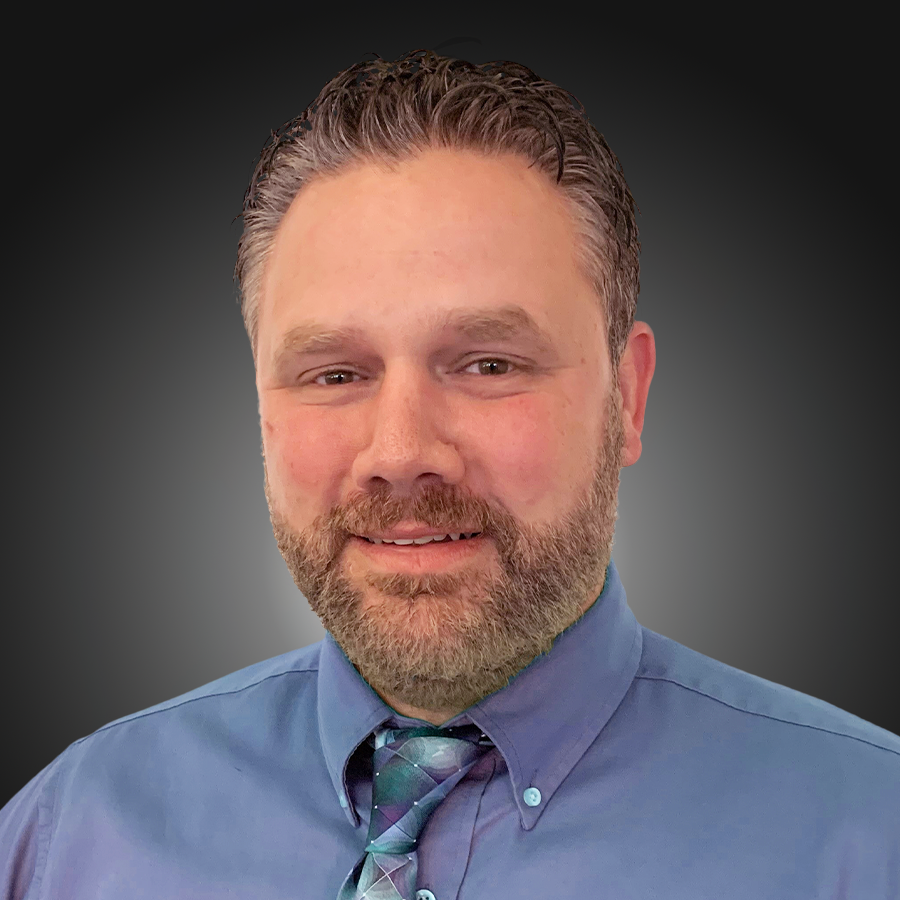
Joshua Asbury
Project Manager, Supply Chain Operations
Josh has 25 years of supply chain planning experience and has been with Simtra BioPharma Solutions for 19 years. In his role, Josh manages the short- and long-term planning and capacity functions. He is responsible for the manufacturing schedule for the Bloomington, Indiana, facility. Josh also helps to manage ERP and MRP functions, material management and week-to-week readiness for production. For pharma and biotech companies, supply chain challenges can emerge at any time. In this interview, Josh discusses the supply chain challenges posed by the COVID-19 pandemic and provides his perspective on how to overcome such issues.
In the post-pandemic environment, what new challenges are you seeing emerge?
During the pandemic, the immediate challenges came from disruption in the procurement and delivery of key supplies. Cleaning supplies, masks, thermometers and even bathroom essentials were just a few of the items that were a challenge to get into manufacturing facilities. An unprecedented amount of time was spent in securing these supplies, which had been taken for granted for so long.
In addition to the struggles of procuring the daily supplies that are critical for a pharmaceutical facility to operate safely, it was increasingly difficult to source other crucial production materials. The lead times for materials doubled and tripled from pre-pandemic timelines.
Shipping and receiving were also affected. Scheduled pickups were constantly rescheduled because of a lack of trucks and drivers. Additionally, incoming and outgoing shipments had too many variables to schedule anything accurately. Because of this, schedules had to be fluid, and capacity had to be protected. This was achieved in many cases by expediting the production of certain batches that were able to run to make room in the schedule for batches that needed to be produced later because of supply chain challenges. Staff shortages across the entire supply chain exacerbated these challenges, putting many companies into severe back order just as demand soared.
Thankfully, there are signs of improvement today. Suppliers are now able to obtain materials to produce what is needed, are no longer forced to prioritize COVID-related orders over everything else, and can manage their distribution of available products, with some suppliers implementing backup locations for production of materials.
From receiving to shipping, from buying materials to procuring drivers to move them, skilled workers are still a challenge to obtain. Outside of the Bloomington, Indiana, manufacturing facility, the challenges of a less-than-ideal workforce complicate visibility and predictability for everything. This includes impacting lead times and scheduling. Visibility is impacted throughout, and no commodity is safe from this because everything is interrelated.
Pharmaceutical and biotech companies are developing more complex medicines such as biologics and vaccines, which need to be maintained at very low temperatures. Many APIs and drug substances must be maintained in the -60 degrees Celsius range and below. These environmental chambers are hard to get and expensive to maintain, and it is difficult to manage capacity and movement. These chambers are also an ergonomic challenge for even the best supply chain teams. This makes the already challenging and critical cold chain that much harder to manage.
How can companies consider evolving with some of the latest supply chain trends?
The combined effect of market forces, the lingering impacts from the pandemic, and a more complex drug development and manufacturing process means that the way the supply chain operates has no choice but to evolve, from supplier selection to inventory management to documentation. For example, organizations that stick to just one supplier for critical materials are increasing their chance of stockouts. In addition, although the pharmaceutical industry is global when it comes to supply, companies should also consider using suppliers close to the location of manufacturing to reduce risk to the overall supply chain.
How are CDMOs positioned to manage potential supply chain hurdles?
CDMOs are, by design, in a better position to quickly change directions and plans. At Simtra BioPharma Solutions, we also have the advantage of expertise around the globe to tap into for improvements in all areas of the business, including the supply chain. In essence, partnering with an established CDMO who is tuned in to trends and changes in the industry is invaluable to the overall health of a supply chain and the success of a project.